Introduction
Venturing into the world of tufted carpet manufacturing requires a comprehensive understanding of the machinery and setup involved. Whether you’re a seasoned entrepreneur or a newcomer to the carpet industry, knowing the right equipment and setup is crucial for producing high-quality tufted carpets. This article delves into the essential machinery and setup required for Tufted carpet manufacturer in UAE, providing detailed insights into each piece of equipment and its role in the production process. By the end of this guide, you’ll be well-equipped with the knowledge needed to set up a successful tufted carpet manufacturing operation.
The Foundation: Setting Up Your Manufacturing Space
Selecting the Right Location
Choosing the appropriate location for your manufacturing facility is the first critical step. The space should be large enough to accommodate all the necessary machinery and allow for smooth workflow. Consider factors such as proximity to suppliers and customers, availability of skilled labor, and compliance with zoning regulations. A well-planned layout can significantly enhance efficiency and productivity.
Preparing the Infrastructure
The next step is preparing the infrastructure. This involves ensuring that the facility has adequate power supply, ventilation, and lighting. Proper flooring is essential to support heavy machinery and facilitate easy movement of materials. Additionally, implementing safety measures such as fire exits, alarms, and emergency protocols is crucial to protect your workforce and equipment.
Essential Machinery for Tufted Carpet Manufacturing
Tufting Machines: The Heart of Production
Tufting machines are the cornerstone of tufted carpet manufacturing. These machines use a series of needles to punch yarn through a backing material, creating loops or cut piles. There are several types of tufting machines, each designed for specific carpet styles and textures.
- Cut Pile Tufting Machines: These machines produce carpets with cut piles, which have a plush, even surface. They use a blade to cut the loops as they are formed, resulting in a soft and luxurious texture.
- Loop Pile Tufting Machines: These machines create loop pile carpets, where the loops remain uncut. Loop pile carpets are known for their durability and resistance to crushing, making them ideal for high-traffic areas.
- Cut and Loop Tufting Machines: These versatile machines can create both cut and loop piles, allowing for intricate patterns and textures. They offer greater design flexibility and are popular for custom and decorative carpets.
Yarn Handling and Feeding Systems
Efficient yarn handling and feeding systems are essential to ensure a continuous and smooth production process. These systems include creels, which hold large spools of yarn, and tensioners, which maintain consistent tension during feeding. Properly managed yarn handling systems prevent yarn breakage and ensure uniform pile height and density.
- Creels: Creels hold multiple spools of yarn and feed them into the tufting machine. They should be designed to accommodate various yarn types and sizes, allowing for quick changes and minimal downtime.
- Tensioners: Tensioners maintain consistent yarn tension, preventing slack and ensuring even tuft formation. Proper tensioning is crucial for achieving uniform pile height and density.
Backing Systems
The backing system provides structural support to the tufted carpet. Primary backing materials, typically made of woven polypropylene or polyester, hold the tufts in place. Secondary backing materials, often made of latex or jute, provide additional stability and durability.
- Primary Backing: The primary backing is the initial layer through which the yarn is tufted. It must be strong and durable to hold the tufts securely. Woven polypropylene and polyester are commonly used for their strength and flexibility.
- Secondary Backing: The secondary backing is applied after tufting to add stability and enhance the carpet’s structural integrity. It is typically made of latex or jute, which provide strength and resilience.
Latex Coating and Drying Equipment
Applying a latex coating to the back of the tufted carpet secures the tufts and enhances the carpet’s durability. The latex coating process involves spreading a layer of latex adhesive onto the back of the carpet and then curing it through a drying process.
- Latex Applicators: Latex applicators evenly distribute the latex adhesive onto the carpet’s backing. The thickness and consistency of the coating can be adjusted to meet specific requirements.
- Drying Ovens: Drying ovens cure the latex coating, ensuring it bonds firmly to the backing and tufts. Proper curing is essential for achieving optimal strength and durability.
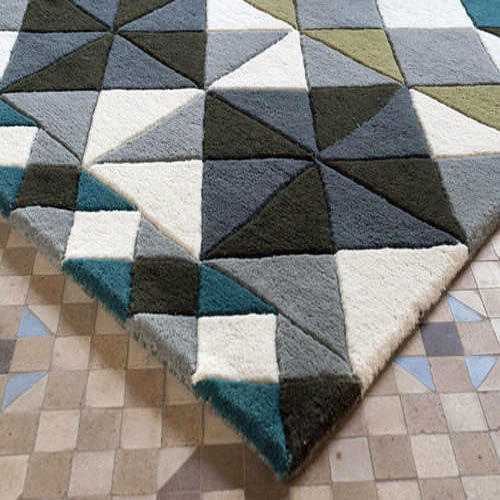
Shearing and Finishing Machines
Shearing and finishing machines are used to trim the carpet’s pile to the desired height and texture. These machines also perform final touches, such as brushing and vacuuming, to enhance the carpet’s appearance and feel.
- Shearing Machines: Shearing machines trim the carpet’s pile to a uniform height, creating a smooth and even surface. They are adjustable to achieve various pile heights and textures.
- Finishing Machines: Finishing machines perform tasks such as brushing and vacuuming to remove loose fibers and enhance the carpet’s texture and appearance. Proper finishing ensures a high-quality final product.
Quality Control and Testing
Inspecting and Testing Yarn
Quality control begins with inspecting and testing the yarn used in tufted carpet manufacturing. Yarn should be tested for strength, elasticity, and colorfastness to ensure it meets the required standards.
- Strength Testing: Yarn strength is tested to ensure it can withstand the tufting process and daily use without breaking.
- Elasticity Testing: Yarn elasticity is tested to ensure it can stretch and recover without losing its shape or causing uneven pile height.
- Colorfastness Testing: Yarn colorfastness is tested to ensure the colors remain vibrant and do not fade or bleed during use or cleaning.
In-Process Inspection
During the tufting process, in-process inspections are conducted to monitor pile height, density, and pattern accuracy. These inspections help identify and address any issues early, ensuring consistent quality.
- Pile Height Inspection: Pile height is measured to ensure it matches the specified requirements. Consistent pile height is crucial for achieving uniform texture and appearance.
- Density Inspection: Pile density is measured to ensure it meets the required specifications. Proper density contributes to the carpet’s durability and comfort.
- Pattern Accuracy Inspection: Pattern accuracy is checked to ensure the design is correctly replicated. Precise pattern accuracy is essential for creating visually appealing carpets.
Final Inspection and Testing
The final inspection and testing involve a thorough examination of the finished carpet to ensure it meets all quality standards. This includes visual inspections, physical tests, and measurements.
- Visual Inspection: The carpet is visually inspected for any defects, such as uneven pile height, loose threads, or color inconsistencies.
- Physical Testing: The carpet undergoes physical tests, such as tensile strength testing, to ensure it meets durability and performance standards.
- Measurements: The carpet’s dimensions are measured to ensure they match the specified requirements. Accurate measurements are essential for proper installation and fit.
Maintenance and Upkeep of Machinery
Regular Maintenance
Regular maintenance of tufting machinery and equipment is crucial for ensuring optimal performance and preventing breakdowns. This includes cleaning, lubrication, and inspection of all moving parts.
- Cleaning: Regular cleaning prevents the buildup of dust and debris, which can affect the machinery’s performance. Proper cleaning ensures smooth operation and longevity.
- Lubrication: Lubrication of moving parts reduces friction and wear, extending the life of the machinery. Proper lubrication ensures efficient and reliable performance.
- Inspection: Regular inspection of machinery helps identify and address potential issues before they cause breakdowns. Proper inspection ensures consistent quality and productivity.
Troubleshooting and Repairs
Having a troubleshooting and repair plan in place is essential for minimizing downtime and maintaining production efficiency. This includes training staff to identify and address common issues and having a reliable repair service available.
- Troubleshooting: Staff should be trained to identify common issues, such as yarn breakage or tension problems, and take corrective action. Proper troubleshooting ensures quick resolution of issues and minimal disruption.
- Repairs: Having a reliable repair service available ensures that major issues can be addressed promptly. Proper repairs ensure the longevity and reliability of machinery.
Conclusion
Setting up and running a tufted carpet manufacturing operation requires a comprehensive understanding of the machinery and setup involved. From selecting the right location and preparing the infrastructure to investing in essential machinery and implementing quality control measures, each step is crucial for producing high-quality tufted carpets. By following this guide, you can ensure that your manufacturing process is efficient, reliable, and capable of meeting the demands of the market.
Investing in the right machinery and setup not only enhances the quality of your products but also improves productivity and profitability. With proper planning, maintenance, and quality control, you can build a successful tufted carpet manufacturing operation that delivers exceptional products and satisfies your customers. Embrace the intricacies of tufted carpet manufacturing and unlock the potential for growth and success in this dynamic industry.
Note :- To Read More Articles Visit on- netblogz